Proactive Maintenance with IoT and AI
페이지 정보

본문
Predictive Maintenance with Internet of Things and AI
In the rapidly changing landscape of industrial and production operations, predictive maintenance has emerged as a game-changer for enhancing asset performance. By utilizing Internet of Things sensors and machine learning algorithms, businesses can now anticipate equipment failures before they occur, minimizing downtime and extending the operational life of machinery. This analytics-based approach contrasts sharply with traditional reactive or scheduled maintenance, offering significant cost savings and workflow efficiency.
IoT sensors are pivotal in this process, collecting real-time data on vital parameters such as temperature, vibration, pressure, and energy consumption. If you adored this article therefore you would like to acquire more info pertaining to Here generously visit our own web site. These sensors transmit data to centralized platforms, where machine learning systems process patterns to identify anomalies. For example, a minor increase in vibration from a motor could signal upcoming bearing failure, allowing technicians to intervene before a severe breakdown happens.
The fusion of AI enhances predictive capabilities by learning from historical data and optimizing its forecasts over time. Advanced techniques like deep learning can handle massive datasets from diverse sources, spotting correlations that manual inspections might miss. For instance, an AI model might detect that a combination of moisture levels and usage time accelerates wear in specific components, enabling targeted maintenance actions.
One of the key benefits of this approach is cost reduction. Unexpected downtime in industries like manufacturing or power generation can cost millions of dollars per hour due to stalled operations and emergency repairs. Predictive maintenance helps organizations shift from a "fix-it-when-it-breaks" mindset to a preventive strategy, slashing maintenance costs by up to 25% and lowering downtime by 50%, according to research reports.
However, deploying predictive maintenance systems is not without challenges. Data accuracy is essential, as inaccurate sensor readings or incomplete datasets can lead to false positives or overlooked warnings. Additionally, integrating legacy systems with state-of-the-art IoT platforms may require significant upgrades or adaptation. Organizations must also address data security concerns, as interconnected devices expand the vulnerability of hacks targeting critical infrastructure.
Looking ahead, the convergence of edge computing and 5G is poised to transform predictive maintenance further. Edge devices can process data locally in real-time, minimizing latency and data transfer requirements. For example, a IoT-enabled sensor on an oil rig could detect a possible pump failure and activate an alert immediately, even in offshore locations with limited connectivity. Meanwhile, 5G technology’s high-speed data transmission allows seamless communication between hundreds of devices in a manufacturing plant, supporting comprehensive predictive analytics.
Another promising development is the integration of virtual replicas with predictive maintenance systems. A digital twin is a real-time digital representation of a physical equipment, enabling engineers to observe its performance and test situations without physical intervention. By merging IoT data with AI-powered digital twins, companies can predict not only when a machine might fail but also how it will fail, enabling precise maintenance strategies.
Despite its complexity, the uptake of predictive maintenance is growing across sectors such as aviation, medical, and utilities. Airlines, for instance, use predictive analytics to monitor engine health and schedule maintenance during routine layovers, preventing costly flight delays. In healthcare, MRI machines and medical equipment equipped with IoT sensors can alert technicians to possible malfunctions before they affect patient care.
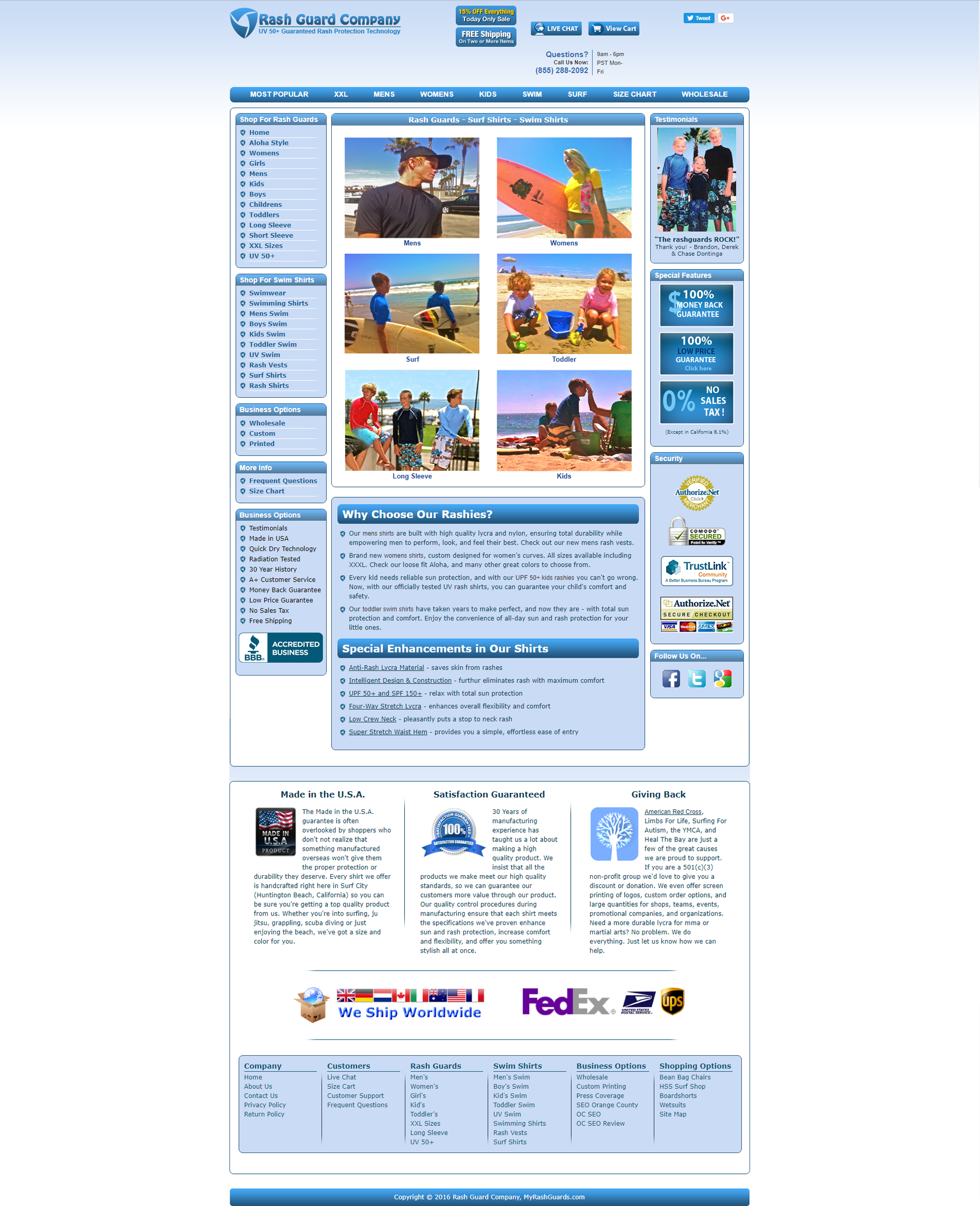
As the innovation evolves, the focus is shifting toward ease of use and scalability. Cloud-based predictive maintenance platforms now offer pre-built templates and user-friendly dashboards, democratizing the technology for mid-sized businesses. Meanwhile, progress in AI explainability are helping build trust in these systems by offering clear insights into how forecasts are made.
Ultimately, predictive maintenance signifies a fundamental change in how industries handle their assets. By harnessing the combined power of IoT and intelligent algorithms, organizations can achieve unmatched levels of operational efficiency, resource conservation, and competitiveness. As these technologies continue to progress, the line between proactive action and predictive intelligence will fade, introducing a new era of intelligent industrial operations.
- 이전글카마그라통관, 시알리스 데이트 강간약 25.06.12
- 다음글가족의 이야기: 사랑과 결속의 힘 25.06.12
댓글목록
등록된 댓글이 없습니다.